A stepper motor is used to achieve precise positioning via digital control. The motor operates by accurately synchronizing with the pulse signal output from the controller to the driver. Stepper motors, with their ability to produce high torque at a low speed while minimizing vibration, are ideal for applications requiring quick positioning over a short distance.
Accurate Positioning in Fine Steps
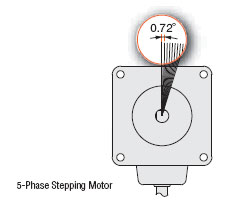
A stepper motor rotates with a fixed step angle, just like the second hand of a clock. This angle is called "basic step angle". Oriental Motor offers stepper motors with a basic step angle of 0.36°, 0.72°, 0.9° and 1.8°. 5-Phase stepper motors offer 0.36° and 0.72°, while 2-Phase stepper motors offer 0.9° and 1.8° step angles.
Utilizing Hybrid Stepper Motor Technology
A hybrid stepper motor is a combination of the variable reluctance and permanent magnet type motors. The rotor of a hybrid stepper motor is axially magnetized like a permanent magnet stepper motor, and the stator is electromagnetically energized like a variable reluctance stepper motor. Both the stator and rotor are multi-toothed.
A hybrid stepper motor has an axially magnetized rotor, meaning one end is magnetized as a north pole, and the other end a south pole. Toothed rotor cups are placed on each end of the magnet, and the cups are offset by half of a tooth pitch.
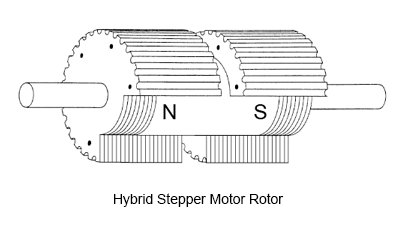
Easy Control with Pulse Signals
A system configuration for high accuracy positioning is shown below. The rotation angle and speed of the stepper motor can be controlled with precise accuracy by using pulse signals from the controller.
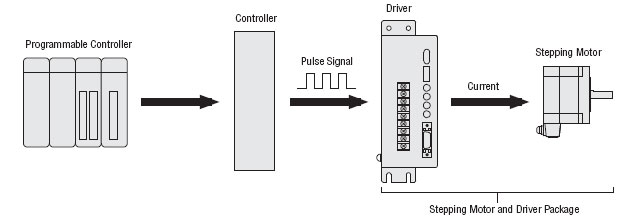
What is a Pulse Signal?
A pulse signal is an electrical signal whose voltage level changes repeatedly between ON and OFF. Each ON/OFF cycle is counted as one pulse. A command with one pulse causes the motor output shaft to turn by one step. The signal levels corresponding to voltage ON and OFF conditions are referred to as "H" and "L" respectively.
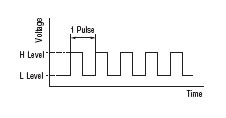
The Amount of Rotation is Proportional to the Number of Pulses
The amount the stepper motor rotates is proportional to the number of pulse signals (pulse number) given to the driver. The relationship of the stepper motor's rotation (rotation angle of the motor output shaft) and pulse number is expressed as follows:
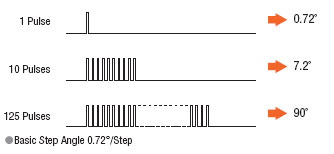
The Speed is Proportional to the Pulse Speed
The speed of the stepper motor is proportional to the speed of pulse signals (pulse frequency) given to the driver. The relationship of the pulse speed [Hz] and motor speed [r/min] is expressed as follows:
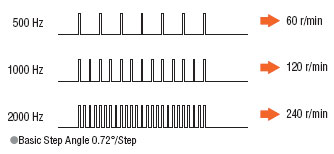
Generating High Torque with a Compact Body
Stepper motors generate high torque with a compact body. These features give them excellent acceleration and response, which in turn makes these motors well-suited for torque-demanding applications where the motor must start and stop frequently. To meet the need for greater torque at low speed, Oriental Motor also has geared motors combining compact design and high torque.
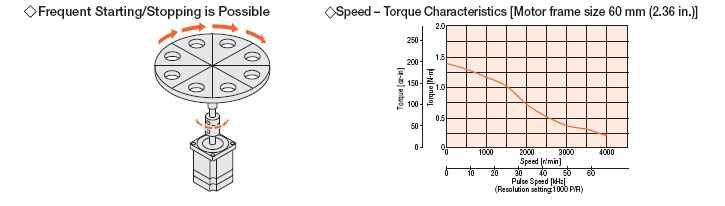
The Motor Holds Itself at a Stopped Positioning
Stepper motors continue to generate holding torque even at standstill. This means that the motor can be held at a stopped position without using a mechanical brake.
Once the power is cut off, the self-holding torque of the motor is lost and the motor can no longer be held at the stopped position in vertical operations or when an external force is applied. In lift and similar applications, use an electromagnetic brake type.
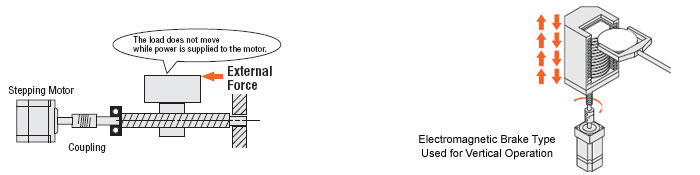